This makes them an ideal choice for machinery applications.
What are INA needle bearings?
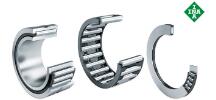
Needle bearings, which are cylindrical roller bearings, are used to avoid friction between surfaces with low rotational speeds.
Because needle roller bearings can be used where There are many different types of needle bearings.
The most common type of needle bearing has an inner race and an outer race.
It also contains needle rollers. Some needle bearings may be used with or without an outer or inner race.
In other cases, the needle rollers within the bearings can work independently.
To make needle rollers effective, they must have the same hardness, accuracy, finish, and speed as the bearing racing.
Because of their small size and high rotation speeds, needle roller bearings are often used in compact mechanisms like gearboxes.
For example, an average car's drive shaft will have eight or more needle bearings.
These bearings can also be used in small appliances, robotics, and aircraft control.
INA needle bearings are cylindrical roller bearings that are used to avoid friction between surfaces with low rotational speeds.
They are more compact than ball bearings and need to be lubricated with oil or grease.
Depending on the application, heavy loads or high speeds may require that bearings receive regular lubrication.
Retainers are essential because needle bearings can operate at high speeds.
The benefits of using INA needle bearings
There are many benefits to using INA needle roller bearings in your applications.
Needle roller bearings have small rollers that reduce friction on a rotating surface, making them ideal for use in applications that need minimal space and weight.
Because of their small size, they can withstand relatively heavy loads without issue.
Additionally, needle roller bearings are more compact than other types of bearings, making them an economical choice for devices that need to be as small as possible.
FINAlly, needle roller bearings are lightweight and can carry a lot of loads at low speeds, making them a great choice for a variety of applications.
How to properly install INA needle bearings
When installing a drawn-cup needle roller bearing, it is important to use the correct tools and procedures to ensure a successful application.
Some general guidelines to follow include:
1. The cup bearing must be pressed into the housing.
2. A standard press must be used with an installation tool. The installation tool should have a back angle of around 15 degrees and be pilot-guided.
3. If the bearing to be installed is a full-compliment type, a detent ball bearing must be placed on the pilot.
4. Keep the housing bore on the same axis.
5. Follow the manufacturer's guidelines to ensure that you are making sure your equipment fits precisely.
6. You can press against the stamped bearing end (typically thicker).
7. Even if you use a good installation tool, the bearing should not be hammered into the housing.
8. The bearing should not be pressed against the housing shoulder.
If a shoulder-shaped housing is required, the bore of the housing must be deep enough to allow the shoulder and fillet to clear the bearing
How to maintain INA needle bearings
Step 1: Selecting the Right Lubrican
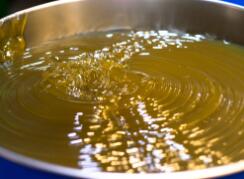
There are a few key things you need to consider when selecting a lubricant for your INA needle bearings.
The most important factor is the operating conditions of your bearings.
You need to choose a lubricant that can reduce friction, corrosion, and contamINAtion while also prolonging the life of your bearings.
There are two main types of lubricants: oils and greases.
Grease lubricants can be used to lubricate needle bearings, but oil lubricants are generally required for high-speed and high-temperature applications.
Consider the composition of the grease lubricant before making your decision.
Additives or thickeners can help you choose the right product for your bearing's operating conditions.
Grease lubricants typically have a National Lubricating Grease Institute grade number, which is determined by the penetration range.
Step 2: Lubricating Your Needle Bearing
There are a few ways to lubricate needle bearings, but the most efficient way is through an automated lubrication system.
Lubricating bearings manually can be done, but it is not as efficient as using an automated system.
Step 3: Knowing When to Relubricate including ball bearings
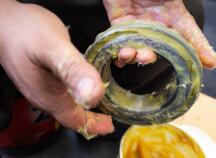
It is important to know when and how to relubricate your bearings.
Different types of lubricants should be used depending on the environment and the load size and speed of the bearings.
Lubrication intervals will vary depending on the application, so it is important to follow the manufacturer's recommendations.
As operating hours increase, degradation of grease lubricants can occur, so it is important to keep track of lubrication intervals and use the correct type of grease.
Oil lubricants will degrade differently depending on the operating conditions, so it is important to be aware of these conditions when determining when to relubricate.
Step 4: Ensuring Proper Mounting of ball bearing
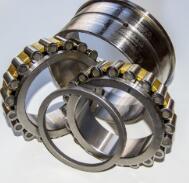
Before mounting needle bearings, it is important to be aware of their tolerances.
The most popular fitting method is the J6/H7 clearance.
There are also guidelines for fitting that you should follow. Additionally, it is important to choose the correct type of shaft.
Bearing manufacturers can make custom shafts for you so that you don't have to worry about choosing the right size or type.
Bearing mounting can be done with either a press fit or a hammer-mounted sleeve, depending on the bore type of the bearing.
If the bearing is large, it will need to be heated before mounting.
Bearings with tapered bores can be mounted on a cylindrical or tapered shaft with an interference fit.
Mounting is usually done with an adapter or withdrawal sleeves.
The type of seat, bearing size, and mounting method will determine the tools that you need.
After mounting your bearing, it is important to inspect it to ensure that it has been properly installed.
Step 5: Continually Inspecting for Signs of Damage
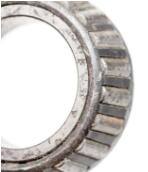
Regular inspection of your bearings is essential for ensuring their longevity.
A regular maintenance plan will help your employees know when to inspect the bearings and when they need to be relubricated.
Poor lubrication, contamINAtion, and improper mounting are the most common causes of bearing failures.
Conclusion
The design of the needle roller bearing should be based on the type of application.
The bearing must be able to handle dynamic and static load conditions, as well as any misalignment or shock loads that are likely to occur.
It should also have adequate lubrication capacity so that it can perform without fail over extended periods of time.
When choosing a needle roller bearing, engineers should consider factors such as radial and axial clearance, external preload, internal clearances, operating speed and temperature range, vibration levels, and cage selection for maximum service life.
All of these considerations will help ensure that the bearing is properly designed for its intended application and runs smoothly for many years to come.