Cylindrical roller bearings-The Definitive Guide (2023)
Cylindrical roller bearings are the go-to when it comes to reliability and durability.
Their unique design makes them essential components for applications that demand long-lasting performance.
Whether you're hauling in a heavy load or grinding away at the race track, they've got your back!
Cylindrical roller bearings have revolutionized the way machines and vehicles move.
Invented in 1794 by Swiss watchmaker Abraham-Louis Breguet, these bearings have emerged as a reliable and efficient component for any machine or vehicle's movement.
With their ability to move in all directions and bear heavy loads, they can be found in everything from bicycles to turbines.
Providing smooth motion without requiring lubrication, cylindrical roller bearings are the perfect solution for any moving application.
Cylindrical roller bearings are commonly used in industrial applications requiring high radial loads.
They consist of an inner and outer ring, with cylindrical rollers held between them.
The rollers have a greater length than the diameter, giving the bearing its cylindrical shape.
These bearings have higher load-carrying capacity than ball bearings, and can also withstand heavy shock loads. In addition, they are less sensitive to misalignment of the shaft compared to ball bearings.
This guide explains the characteristics of cylindrical roller bearings, as well as their applications, components, advantages, and disadvantages.
Definition of cylindrical roller bearings
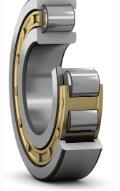
Cylindrical roller bearings are a type of rolling-element bearing that uses cylinders as the rolling element.
These bearings help to reduce friction and support radial loads, making them ideal for high radial-load applications.
Cylindrical roller bearings have two rings, an inner and an outer, with cylindrical rollers in between.
They are made from heat-treated steel or brass and come in various sizes and configurations depending on the application they are used for.
Cylindrical roller bearings can support axial loads in both directions, making them suitable for heavy-duty applications such as motors, compressors, conveyor systems, and other industrial machinery.
As well as being durable and reliable, these bearings have a low coefficient of friction which helps to improve efficiency and reduce wear.
Proper maintenance is essential for prolonging the life of cylindrical roller bearings
Types of cylindrical roller bearings
-
Single-row
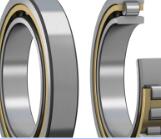
Single-row roller bearings are designed with a single row of rolling elements that can handle radial and axial loads.
Typically, the inner ring has two shoulders and the outer ring has one shoulder.
These bearings provide a high level of stiffness while allowing for low-friction operation. Single-row roller bearings are commonly used in transmissions, conveyor belts, agricultural machinery, construction equipment, and heavy-duty industrial applications.
They are also suited to applications where there is a need for increased radial loading capacity or reduced axial space requirements.
In addition to the different designs available, single-row roller bearings come in various sizes and materials that can be tailored to specific application needs.
Single-row roller bearings can offer many advantages over other types of rolling element bearings including improved reliability, improved accuracy, and higher load-carrying capacity.
-
Double row
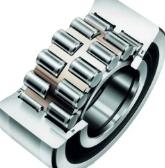
A double-row roller bearing is a type of bearing that has two rows of rolling elements in a single housing.
It has a higher load capacity than a single-row bearing and is mainly used in applications where radial and axial loads need to be supported simultaneously.
Its design enables it to handle greater amounts of thrust loads compared to other types of bearings, such as ball bearings or needle bearings.
In addition, it is capable of accommodating misalignments caused by shaft deflections and thermal expansion.
This makes the double-row roller bearing an ideal choice for high-load, high-precision applications, such as gears, turbines, and motors.
These components provide superior performance by minimizing friction and allowing for smooth operation with minimal maintenance requirements.
-
Multi-row
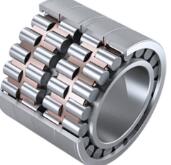
Multi-row roller bearings are designed to accommodate heavier radial and axial loads, as they are composed of several rows of rollers.
They also provide higher stiffness than single-row roller bearings due to the increased number of rolling elements.
Additionally, the cage used in multi-row roller bearings is optimized for improved centering accuracy, making them suitable for applications such as gearboxes and turbines.
In some cases, multi-row roller bearing designs include features such as grooves or pockets on the inner or outer rings which allow lubrication to be fed directly into the bearing area while it is still rotating.
This helps to maintain optimal performance and reduce wear over time.
Components of a cylindrical roller bearing
-
Inner ring
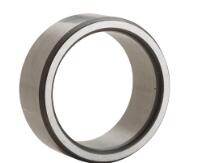
The inner ring of a cylindrical roller bearing is one of the two rings that make up the basic bearing component.
It contains an array of cylindrical rollers which are arranged perpendicular to the axis of the bearing's inner and outer races.
The inner ring is typically mounted on a shaft or another type of rotating member, while the outer race rotates with it to reduce friction between them.
The inner ring also acts as a contact surface for the lubricant used to ensure smooth operation and helps provide load-carrying capabilities.
The choice of material for the inner ring depends on its use; some common materials used are steel, brass, aluminum, bronze, and thermoplastic polymers.
-
Outer ring
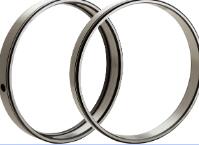
The outer ring is the component of a cylindrical roller bearing that provides a rolling contact surface for the rollers.
It is usually made from bearing steel and features an annular groove, which helps to hold lubricant for reduced friction during operation.
Additionally, it can provide radial load-bearing capability as well as improved stiffness and dimensional accuracy.
The outer ring also serves to keep the rollers in alignment with one another and stop them from separating.
Finally, its design prevents dirt or debris from entering the bearings and potentially damaging them.
-
Cylindrical rollers
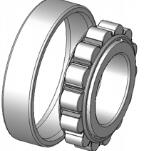
Cylindrical rollers are the most commonly used roller type in cylindrical roller bearings.
They have tapered ends and are typically made from chrome-plated steel.
The shape of these rollers allows them to handle radial loads as well as thrust loads applied at right angles to their length.
Moreover, they reduce frictional force and enable the bearing to run smoothly with minimal noise and vibration.
This makes them an ideal choice for applications that require a quiet operation or high-speed rotation.
In addition, they provide superior corrosion resistance, making them ideal for use in damp environments.
As a result, cylindrical rollers are widely used in automotive, industrial, and medical equipment applications.
-
Cages
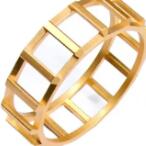
Cages are an integral component of cylindrical roller bearings.
They help to evenly space the rollers along the bearing's inner and outer rings, allowing for greater contact area and smooth operation.
Cages also provide a measure of protection against shock loads and contaminants from entering the bearing, helping to increase its lifespan.
As such, it is important to select cages that are compatible with your application requirements.
Common materials used for cages include steel, plastic, and nylon. Each material offers unique benefits when it comes to performance and durability.
Steel cages offer excellent strength and corrosion resistance, while plastics offer greater impact resistance and better thermal properties compared to metals.
Nylon cages are typically preferred in applications where noise reduction is desired or where precision parts must be handled.
Application of cylindrical roller bearing
-
Oil and gas
Cylindrical roller bearings are commonly used in oil and gas applications, such as compressors and pumps, where their superior radial load-carrying capacity makes them ideal for the high-pressure environments often encountered.
They also have a relatively low friction coefficient, meaning that they require less energy to operate, reducing operating costs.
Additionally, their robust design ensures long life and reliability even in extreme temperatures and with heavy loads.
Their ability to rotate around the axial axis makes them particularly suitable for applications where rotation is required or advantageous.
This means they can be used on turbines, motors, generators, and other rotating equipment.
-
Gearboxes
Cylindrical roller bearings are the preferred choice of most gearbox manufacturers due to their reliability and ability to handle large radial loads.
The construction of cylindrical roller bearings allows them to be robust and resistant to damage, even under extreme conditions of shock or vibration.
In addition, they can provide an increased level of safety as they have a wide range of operational speeds, which means that they can be used in high-speed applications without losing performance.
Finally, the low friction coefficient of cylindrical roller bearings makes them more efficient than ball-bearing designs for transmitting power.
With these factors combined, it is no wonder why cylindrical roller bearings are so widely used in gearboxes around the world.
-
Wind turbines
Cylindrical roller bearings are an integral component of wind turbines due to their ability to support large radial and axial loads, as well as handle impacts from the highly dynamic nature of the turbine blade vibration.
They also offer long service life with no need for lubrication or maintenance, making them a cost-effective choice for such applications.
Furthermore, cylindrical roller bearings have low friction characteristics, which help reduce wear on components under high-speed operation and improve the energy efficiency of the turbine.
As such, they are often used in conjunction with other bearing types to deliver optimal performance.
All these features make cylindrical roller bearings an ideal choice for wind turbine applications.
-
Machine tool
Cylindrical roller bearings are widely used in machine tool applications, due to their ability to carry high radial loads and moderate thrust loads.
In addition, the rollers are designed for low-friction operation, which helps reduce noise and vibration levels during operation.
Furthermore, cylindrical roller bearings have a higher dynamic load capacity than ball bearings, making them ideal for high-speed applications.
The design also allows for easy installation and maintenance with minimal effort required.
As such, they are often seen as an excellent choice when it comes to selecting bearing solutions for machine tools.
Cylindrical roller bearings provide superior performance in machine tool operations due to their increased load capacity and reduced noise and vibration levels.
-
Electric motors
Cylindrical roller bearings are widely used in electric motors due to their excellent load-carrying capacity and stiffness, as well as their ability to operate at high speeds with low noise levels.
The design of the bearing ensures that it can withstand radial loads, thrust loads, and moments, making them perfect for applications where motors need to run reliably and efficiently.
The separable inner and outer rings also allow for easier installation compared to traditional ball bearings.
In addition, they have a low-temperature rise which reduces heat generation within the motor.
This makes them an ideal choice for applications where prolonged periods of operation are necessary.
Ultimately, cylindrical roller bearings provide improved performance, durability, and reliability in electric motors thanks to their superior design characteristics.
-
Material handling
Cylindrical roller bearings are used in a wide range of material handling applications due to their ability to carry heavy loads at low speeds.
They have higher load capacity than other bearing types and can operate with minimal vibration in high-speed operations.
Their ability to withstand extreme temperatures and long-term usage makes them an ideal choice for transporting items in various industries such as mining, manufacturing, construction, and transportation.
Additionally, cylindrical roller bearings are corrosion-resistant and require little maintenance which helps increase the lifespan of the product.
Overall, they provide optimal performance while standing up to constant use over time. As a result, these bearings are widely used in many different material handling systems today.
-
Pumps
Cylindrical roller bearings are widely used in the industry for pumps.
Their capacity for radial load and axial load is higher compared to other similar bearing types, due to their inner and outer rings having linear contact surfaces with rollers arranged perpendicular to them.
This makes cylindrical roller bearings ideal for applications that require high-speed rotation or heavy loads, such as pumps which often bear large amounts of pressure.
The design of cylindrical roller bearings also allows them to accommodate both static and dynamic misalignment, making them reliable under varying conditions and environments.
Moreover, they have a long service life even when exposed to dust or debris-filled environments and are highly resistant to shock loads.
-
Steel mills
Cylindrical Roller Bearings are widely used in steel mill applications due to their durability and load-bearing capacity.
These bearings are ideal for high radial loads, because of their cylindrically shaped rollers, which allow them to be equally loaded from all directions.
Furthermore, the rollers provide an even distribution of pressure on the inner and outer raceways of the bearing, creating a stable system with minimal noise or vibration.
Additionally, Cylindrical Roller Bearings have low friction characteristics, allowing them to operate efficiently while reducing the amount of energy needed during operation.
This makes them a cost-effective solution for many steel mills as they reduce maintenance costs and extend the life cycle of the machinery.
Advantages of cylindrical roller bearings
-
High load-carrying capacity
Cylindrical roller bearings are designed to carry heavy radial loads and are capable of operating at high speeds.
They feature two rows of cylindrical rollers, which make them well-suited for applications that require high radial loads as opposed to thrust loads.
The design also makes them more compact than other types of roller bearings and helps to reduce friction and wear.
The rollers also maintain uniform contact with the raceway, reducing vibration and noise.
-
High-speed capability
Cylindrical roller bearings are renowned for their ability to operate at high speeds. Thanks to their unique design, they can handle higher revolutions per minute (RPM) than other types of roller bearings.
This makes them suitable for applications where speed is a critical factor, such as in the automotive and aerospace industries.
The construction of cylindrical roller bearings also provides superior radial and axial load capacity, allowing them to withstand considerable forces.
-
Low friction and low heat generation
Cylindrical roller bearings are highly versatile and can be used in a variety of applications.
They offer several advantages, such as low friction and low heat generation, that make them ideal for use in high-speed and high-load applications.
These bearings also have a relatively large contact area between the inner and outer ring rolling elements which facilitates greater load-carrying capacity.
Additionally, they have a higher radial load capacity and dynamic load-carrying capacity compared to other types of bearings.
-
Low noise and vibration
Cylindrical roller bearings are the preferred choice for applications requiring low noise and vibration.
Their design not only reduces noise and vibration but also provides greater radial load capacity than other types of bearings.
Additionally, cylindrical roller bearings can accommodate heavy misalignment as they feature an inner ring and outer ring that are both slightly convex or concave, allowing the rollers to move freely within their respective rings.
Disadvantages of cylindrical roller bearings
-
Sensitive to misalignment
Cylindrical roller bearings are highly sensitive to misalignment, which can result in excessive wear and tear on the bearing's components.
In extreme cases, it can even cause catastrophic failure of the bearing or its associated components.
This makes them unsuitable for applications where accuracy is critical or tolerances must be maintained to a very high standard.
-
Require high initial load
Cylindrical roller bearings tend to require a high initial load, which can increase the cost of installation and operation.
This type of bearing is often used in heavy-duty industrial machinery that must withstand large loads, such as those found in steel plants or paper mills.
High initial loads can also lead to wear and tear more quickly than other types of bearings, reducing the lifespan of a machine.
Conclusion
In conclusion, cylindrical roller bearings are a reliable and cost-effective solution for many different applications.
They offer excellent performance in both light and heavy-duty operations as well as providing superior vibration-dampening qualities.
They are also extremely versatile, allowing for a wide range of installation requirements depending on the application.
With proper maintenance and care, cylindrical roller bearings can provide years of reliable service.