Needle roller bearings: Everything you want to know!
Needle roller bearings--the perfect solution for all your applications! Uncover the basics, learn about design considerations, and discover the advantages of using needle roller bearings for a variety of applications.
Are you looking for the perfect bearing to support your application? Needle roller bearings may be the solution. Learn everything you need to know about needle roller bearings in this comprehensive guide.
Needle roller bearings are cylindrical roller bearings with relatively small diameters. They are used to support radial loads and are used in a variety of automotive and industrial applications.
They offer high precision, low noise, and low friction, so they are well-suited for use in high-speed applications.
Needle roller bearings have become a popular choice for many applications due to their low cost, compact size, and high load capacity.
In this article, we'll explore the benefits of using needle roller bearings and how to install them correctly.
Introduction to needle roller bearings
Needle roller bearings are a type of roller bearings that utilize small cylindrical rollers which are typically of a larger diameter than the bore of the bearing.
They are designed to reduce the amount of friction and provide support for radial and axial load-bearing applications.
Needle roller bearings are generally found in various types of industrial machinery, including pumps, engines, and conveyors.
Due to their low cost and high load capacity, they are a popular choice for various applications.
Types of needle roller bearings
-
Needle roller and cage assemblies
Needle roller and cage assemblies are precision-manufactured components consisting of small-diameter cylindrical rollers and a cage that contains and separates them, enabling them to freely move within the cage.
-
Drawn cup needle roller bearings
Drawn cup needle roller bearings are roller bearings with thin-walled, drawn outer shells that have high load capacity and high accuracy.
The bearings have a low sectional height and are typically used with axial guidance in applications where radial space is limited.
They are used in automotive and industrial applications, such as transmission, steering, and suspension components.
-
Needle roller bearings with machined rings
Needle roller bearings with machined rings are used in a wide range of applications, from automotive to industrial equipment.
They offer an advantage over conventional bearings owing to their small size, high load capacity, and low friction.
They are designed with high-precision machined inner and outer rings, tightly packed needle rollers, and a cage to maintain roller alignment.
This construction allows for high radial and axial stiffness, low rotational torque, and low friction.
-
Alignment needle roller bearings
Alignment needle roller bearings are used in applications requiring high accuracy and minimum radial load.
They feature an outer race with an inner race offset from the centerline.
This offset allows for smooth, low-friction operation of the bearing and increases the accuracy of its movement.
The inner race is fitted with an array of needles that roll between the outer race and the inner race.
This design ensures a smooth and efficient transfer of power, resulting in reduced wear and tear on the bearing.
-
Combined needle roller bearings
Combined needle roller bearings are a type of roller bearing that combines two sets of needle rollers with a single outer race.
They are suitable for use in applications with limited space and are typically used in automotive and industrial applications.
-
Universal joint bearings
Universal joint bearings are precision components used to transmit rotary motion from one shaft to another while accommodating angular misalignment.
They are typically used to connect two shafts at various angles, allowing smooth, vibration-reducing operation.
They are versatile, durable, and require minimal maintenance.
-
Needle roller bearing components
Needle roller bearing components include a needle bearing, a thrust bearing, a cage, and a shaft.
The needle bearing is a cylindrical roller bearing with a small diameter and high load capacity.
The thrust bearing has a flat, thin profile and is used to absorb axial loads.
The cage holds the rollers in place and ensures proper alignment.
The shaft is the main support to which the needle roller-bearing components are attached.
Application of needle roller bearings
-
Automotive
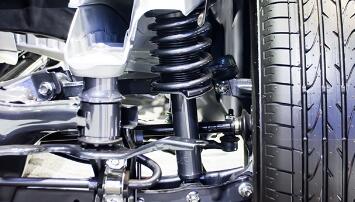
Needle roller bearings are used in the automotive industry in applications such as camshafts, rocker arms, and crankshafts.
They are used in the transmission to reduce friction and provide a smoother operation.
They are also used in the suspension system to reduce vibration and increase load capacity.
-
Lawn and Garden Equipment
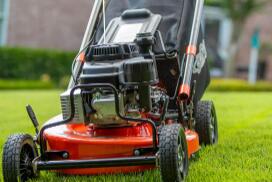
Needle roller bearings are used in lawn and garden equipment to reduce friction and ensure smooth operation.
The small size of the bearing helps reduce weight in the equipment and also makes it easier to install.
-
Machine Tool
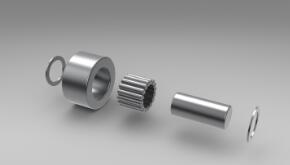
Needle roller bearings are used in many machine tools, such as milling machines, lathes, and grinders.
They are often used in spindles and feed screws, as they provide a low-friction, low-wear solution for these high-precision applications.
Needle roller bearings are also used in high-speed applications, such as headstocks and tailstocks, where they provide smooth, accurate operation.
-
Oil & Gas
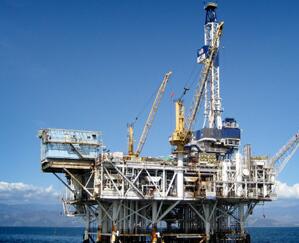
Needle roller bearings are excellent for applications in oil and gas components such as pumps, valves, compressors, and turbines.
Additionally, they are used in rotary and linear motion applications.
-
Power Tools
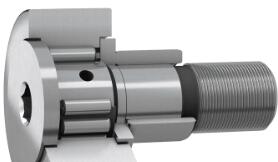
Needle roller bearings are used in power tools such as drills, saws, grinders, and more.
They are designed to handle high axial and radial loads, and because of their small size, they can fit into tight spaces.
They are also more efficient and require less maintenance, making them ideal for power tools.
-
Primary Metals
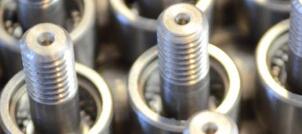
Needle roller bearings are used in primary metals for applications involving high radial loads and low axial loads such as roll neck bearings and rollers in rolling mills.
They can also be used in conveyor systems and other applications requiring high-speed rotation and long service life.
Needle roller bearings are also used in transfer line equipment for the continuous casting of steel.
-
Printing Machines
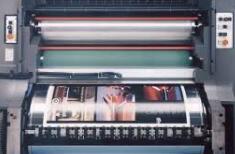
The bearings help in providing smooth and precise movement of the printing drums and also help in reducing the noise and vibration generated due to the movement.
It also helps in reducing the energy consumption of the machine by reducing the friction between the printing drums and the needle roller bearing.
Advantages of needle roller bearings
-
High load-carrying capacity
Needle roller bearings have a high load-carrying capacity and are suitable for heavy-duty applications and can handle radial loads and axial loads in one direction and are capable of carrying dynamic and static loads. Needle roller bearings have a large surface area for contact with the raceways, giving them a high load-carrying capacity.
-
Compact size and low weight
Needle roller bearings are characterized by their compact size and low weight.
They have a small diameter, which allows them to fit into tight spaces, while their low weight makes them ideal for applications where weight is a concern.
-
High stiffness and accuracy
Needle roller bearings have high stiffness and accuracy because of their low rotational friction, high load capacity, and precision manufacturing.
The unique design of needle rollers ensures that the load is evenly distributed throughout the bearing, preventing uneven wear and ensuring a high degree of accuracy.
-
Low friction and low noise
Needle roller bearings offer a smooth and quiet operation due to their thin cross-section, allowing them to roll more freely than other types of bearings.
Selection and maintenance of needle roller bearings
-
Factors to consider when selecting needle roller bearings (e.g. load, speed, size, operating conditions)
When selecting needle roller bearings, it is important to consider the load, speed, size, and operating conditions.
The load rating determines the maximum load the bearing can safely handle, the speed rating determines the maximum speed the bearing can safely operate and the size determines the space available for the bearing.
Operating conditions such as temperature, vibration, and lubrication also need to be taken into consideration.
-
Proper installation and handling of needle roller bearings
Needle roller bearings should be handled and installed carefully to ensure proper performance.
Make sure the bearings are clean and free from dirt or debris.
Check the bearing clearance and the proper torque of the nut before installation.
Check the bearing alignment and the proper fit to the mating parts. Inspect the bearing after installation to make sure it is secure and functioning properly.
-
Lubrication and maintenance requirements
Needle roller bearings need regular lubrication and maintenance to ensure their optimal performance.
It is important to use the correct lubricant and apply the proper amount of grease to the bearing.
Additionally, it is important to regularly inspect the bearing for signs of wear or damage.
If any are found, the bearing should be replaced immediately.
Conclusion
Needle roller bearings are a great solution for applications that require high load capacity, space-saving, and low cost.
They are highly efficient and offer superior performance in challenging operating conditions.
With their wide variety of designs, they are suitable for a range of applications and are sure to provide the best fit for any application.